MEMBRANE FILTRATION
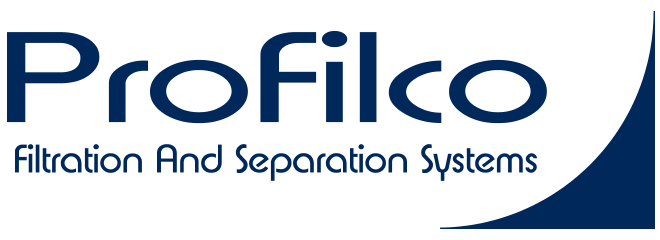
Profilco's filtration technology is now part of Techlink
Porous PTFE membranes (pPTFE or ePTFE) consist of expanded PTFE sheets or tubes that have a controlled porosity of the order of 100 nm to 1µ. Because of the outstanding chemical resistance, and “non-stick” property of PTFE, they form interesting filtration media for a horde of applications, many of which in the chlor-alkali and related industries. With our acqusition of PROFILCO of the Netherlands, TECHLINK builds turn-key, single step brine filtration systems based on Tefflux® micrometric membrane technology and back-pulse membrane cleaning.
TEFFLUX® Micro-Filtration Membranes
TEFFLUX® micrometric pPTFE membranes technology comes from the USA. They are seamless tubes of about 15mm diameter of expanded PTFE. The absence of seams is a strong guarantee against failures of membranes. The tubes are mounted on PP cylinders, and assembled in sets of nine, which more or less replicate the dimensions of a classic candle. For this reason, the Tefflux® micrometric membranes can be retrofitted in existing filter vessels using existing tube sheets. Alternatively, new vessels and tube sheets may be supplied made of titanium, FRP and other corrosion-free materials.

Single elements are grouped in clusters of nine, which are introduced though the tube-sheet from the top, which avoids having to lift the tube-sheet to replace candles. The filtration vessels most often have an open top, because the downstream pressure may be atmospheric in most cases.
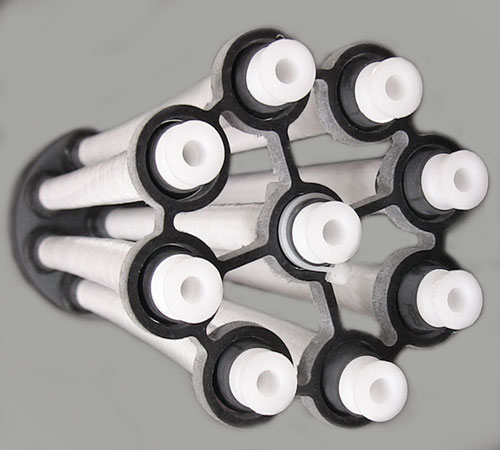


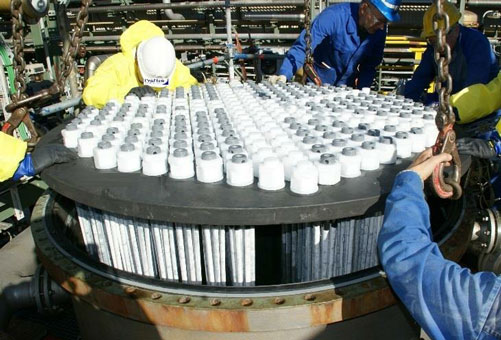
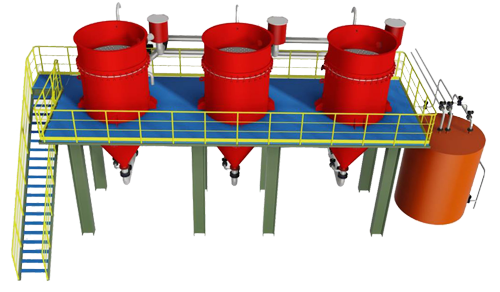

Single-step membrane filtration for calcium & magnesium removal
Classic brine preparation
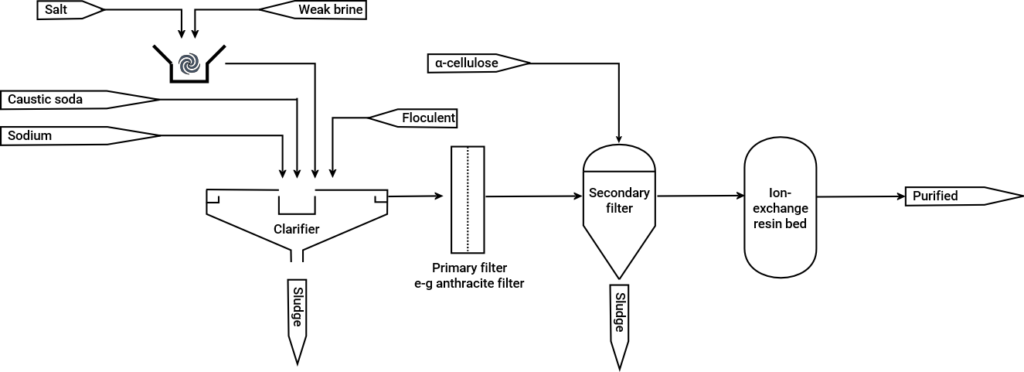
Brine preparation with Tefflux
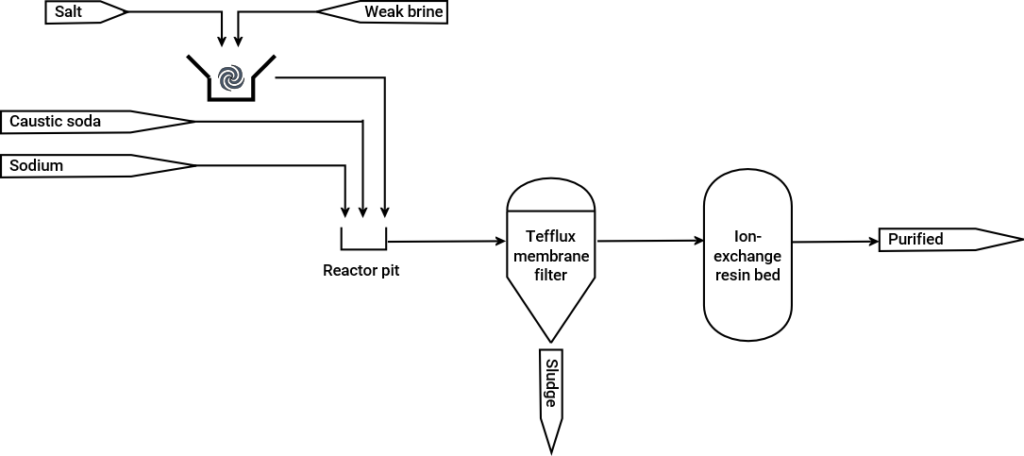
Brine preparation with one-step micro-filtration with TEFFLUX® back-pulsed membranes
- Settler no longer needed
- α-cellulose no longer needed
- Floculent no longer needed
- Primary filtration (anthracite) no longer needed
- Automatically operates and does not require labour
- Replace the membranes twice in twenty years only
Magnesium rich sea salt
Magnesium rich sea salt sets a challenge to classic brine preparation systems, because the magnesium hydroxide does not separate in the settler if the concentration of magnesium is too high. The maximum ratio is usually deemed to be 1 part of magnesium to 2.5 parts of calcium by weight. Magnesium rich salts require the addition of a costly floculent and a longer residence time in the settler.
On the other hand, magnesium hydroxide is difficult to filter out, because it forms a sticky slime on filter candles, which does not break away during backflush cycles.
Techlink and Profilco have therefore developed a special method to purify magnesium rich salts using Tefflux® micrometric membrane filtration, without addition of any floculent and without wasteful prior salt washing.
Single-step membrane filtration for calcium chloride plants
Concentrated HCl and Calcium carbonate are mixed and react to form CaCl2.A large part of the CaCO3 does remains unreacted as this is dosed in excess. It needs to be filtered out from the CaCl2 solution.
In the legacy design, the solution enters a settler after pH neutralization and a polymer is added to enhance the settling process. The overflow is filtered by a filter press, and/or a precoat filter using alpha-cellulose as body feed.
Our TEFFLUX membrane filter can filter the CaCl2 solution without a settling step, and without addition of any floculent or body-feed. The sludge seems creates a nice filter cake on the membranes, that is easily discharged during short back-pulse cycles. The sludge from the filter can be recycled to the reactor, and does not contain any added organic material. The filtrate turbidity is very low ( < 05 NTU) and can be directly sent to the evaporator section.
Classic calcium chloride process
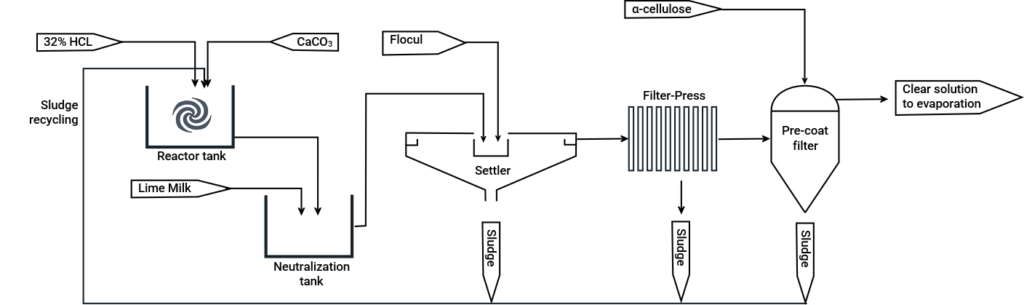
Calcium chloride process with Tefflux
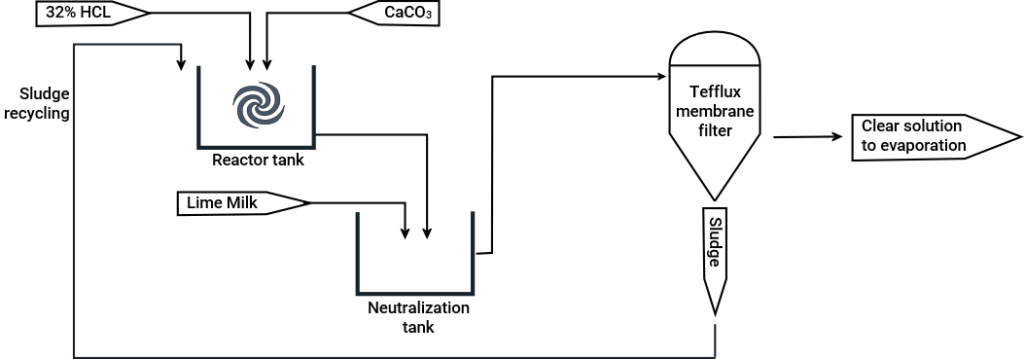
CaCl2 process with one-step micro-filtration with TEFFLUX® back-pulsed membranes
- Settler no longer needed
- α-cellulose no longer needed
- Floculent no longer needed
- Automatically operates and does not require labour
- The sludge produced is clean and free from added organic material (e-g body feed).
Filters for sodium chlorate and sodium hypo
Based on the TEFFLUX® micrometric pPTFE membranes.
- No pre-coat required
- Reduces waste disposal cost
- Simplified automation
- Maximum product clarity
- Minimum operating & maintenance cost